An engine wheel is a crucial component of an engine, responsible for converting the reciprocating motion of the piston into rotational motion. It is usually made of cast iron or forged steel and has a rim with teeth, called the flywheel ring gear, which engages with the starter motor to start the engine.
The engine wheel plays a vital role in the smooth operation of the engine. It stores kinetic energy during the power stroke and releases it during the exhaust and intake strokes, ensuring continuous rotation of the crankshaft. This helps to overcome the uneven torque produced by the piston and maintain a consistent speed.
Engine wheels have been used in various forms for centuries, with early examples found in watermills and windmills. In modern engines, they are typically integrated with the crankshaft and enclosed within the engine block for protection and efficiency.
Engine Wheel
The engine wheel is a vital part of an engine, responsible for converting reciprocating motion into rotational motion. Key aspects of the engine wheel include:
- Material: Typically made of cast iron or forged steel for durability and strength.
- Shape: Usually circular with a rim and teeth (flywheel ring gear) for engaging with the starter motor.
- Location: Located within the engine block, connected to the crankshaft.
- Function: Stores and releases kinetic energy to ensure smooth engine operation.
- Size: Varies depending on the size and power of the engine.
- Balance: Precisely balanced to minimize vibrations and ensure efficient operation.
In conclusion, the engine wheel plays a crucial role in the performance and efficiency of an engine. Its material, shape, location, function, size, and balance are all critical factors that contribute to its overall effectiveness. Understanding these aspects is essential for engineers and mechanics involved in engine design, maintenance, and repair.
1. Material
The choice of material for engine wheels is crucial for ensuring their durability and strength, which are essential for reliable engine operation. Cast iron and forged steel are commonly used due to their inherent properties and ability to withstand the demanding conditions within an engine.
- Durability: Cast iron and forged steel possess high durability, enabling them to endure the constant stress and wear associated with engine operation. They can withstand repeated cycles of heating, cooling, and mechanical loading without compromising their integrity.
- Strength: These materials exhibit high tensile strength, yield strength, and fatigue strength. They can the immense forces generated during combustion and effectively transmit power from the piston to the crankshaft.
- Resistance to Wear: The hardness and wear resistance of cast iron and forged steel help the engine wheel resist caused by friction and contact with other components. This ensures long-lasting performance and reduces the need for frequent maintenance or replacement.
- Heat Resistance: Engine wheels are subjected to high temperatures during engine operation. Cast iron and forged steel have good heat resistance, allowing them to withstand these temperatures without losing their strength or becoming deformed.
In summary, the use of cast iron or forged steel for engine wheels is essential for ensuring their durability, strength, wear resistance, and heat resistance. These properties contribute to the overall reliability and efficiency of the engine, making them suitable for various applications in vehicles, machinery, and industrial equipment.
2. Shape
The shape of an engine wheel, typically circular with a rim and teeth (flywheel ring gear), is crucial for its functionality and connection to other engine components. The circular shape provides a stable and balanced platform for the wheel to rotate smoothly, minimizing vibrations and ensuring efficient power transmission.
The rim of the engine wheel serves as the contact surface for the flywheel ring gear, which is engaged by the starter motor to start the engine. The teeth on the flywheel ring gear provide a positive engagement with the starter motor's pinion, ensuring that the engine crankshaft is rotated and the engine is started.
The shape and design of the engine wheel allow for efficient transfer of power from the piston to the crankshaft. The circular motion of the wheel converts the reciprocating motion of the piston into rotational motion, which is then transmitted to the crankshaft and other engine components.
In summary, the shape of the engine wheel, characterized by its circular form, rim, and teeth, is essential for its proper functioning within the engine. It enables the engagement with the starter motor, facilitates the conversion of reciprocating motion to rotational motion, and contributes to the overall efficiency and reliability of the engine.
3. Location
The location of the engine wheel within the engine block and its connection to the crankshaft are crucial for its proper functioning and the overall performance of the engine. The engine block is the main structural component of the engine, housing the cylinders, crankshaft, and other critical components. By being located within the engine block, the engine wheel is securely positioned and protected from external factors that could affect its operation.
The connection between the engine wheel and the crankshaft is achieved through a splined or keyed joint, ensuring that the two components rotate in unison. This connection allows the engine wheel to transmit the reciprocating motion of the piston to the crankshaft, converting it into rotational motion. The crankshaft then transfers this rotational motion to other engine components, such as the camshaft, transmission, and wheels.
The precise location and secure connection of the engine wheel are essential for maintaining proper engine timing and ensuring efficient power transfer. Any misalignment or looseness in this connection can lead to reduced engine performance, increased wear and tear, and potential engine damage. Regular maintenance and inspection of the engine wheel and its connection to the crankshaft are crucial to ensure the longevity and reliability of the engine.
4. Function
The engine wheel plays a crucial role in ensuring smooth engine operation by storing and releasing kinetic energy during the engine cycle. As the piston moves up and down within the cylinder, it imparts force on the connecting rod, which is connected to the engine wheel. During the power stroke, when the piston is moving down and compressing the air-fuel mixture, the engine wheel stores kinetic energy. This stored energy is then released during the exhaust and intake strokes, when the piston is moving up, ensuring continuous rotation of the crankshaft.
The storage and release of kinetic energy by the engine wheel helps to overcome the uneven torque produced by the piston during the different stages of the engine cycle. Without the flywheel's inertia, the engine would experience sudden bursts of speed during the power stroke and slow down during the exhaust and intake strokes, resulting in rough and inefficient operation.
The size and weight of the engine wheel are carefully designed to match the specific requirements of the engine. A heavier flywheel stores more kinetic energy and provides greater smoothness, but it can also increase the overall weight and inertia of the engine. Engineers must carefully balance these factors to achieve optimal performance and efficiency.
In summary, the function of the engine wheel as a kinetic energy store is essential for smooth and efficient engine operation. It helps to overcome the uneven torque produced by the piston, ensuring continuous rotation of the crankshaft and reducing vibrations. Understanding this function is crucial for engineers designing and maintaining engines, as it directly impacts the overall performance, reliability, and durability of the engine.
5. Size
The size of an engine wheel is directly related to the size and power of the engine it is designed to operate with. Larger and more powerful engines require larger engine wheels to handle the increased forces and store more kinetic energy. The size of the engine wheel is a critical factor in ensuring smooth and efficient engine operation.
A larger engine wheel has a greater moment of inertia, which means it can store more kinetic energy. This stored energy helps to smooth out the fluctuations in torque produced by the engine's pistons, resulting in more stable and consistent power delivery. In larger engines, which typically have more cylinders and higher displacement, the increased mass and power output require a larger engine wheel to maintain smooth operation.
The relationship between engine size, power, and flywheel size is evident in various applications. For example, in high-performance racing engines, larger and lighter flywheels are used to store more kinetic energy and improve engine response. Conversely, in heavy-duty diesel engines used in trucks and construction equipment, larger and heavier flywheels are employed to handle the high torque and low-speed operation of these engines.
Understanding the connection between engine size, power, and flywheel size is crucial for engineers designing and optimizing engines. By carefully selecting the appropriate flywheel size, engineers can ensure that the engine operates smoothly and efficiently, delivering optimal performance and durability.
6. Balance
In the context of engine wheels, balance is critical for minimizing vibrations and ensuring efficient operation. An unbalanced engine wheel can cause excessive vibrations, leading to premature wear and tear of engine components and reduced overall performance.
- Static balance: Static balance ensures that the engine wheel does not wobble when placed on a flat surface. This is achieved by distributing the mass of the wheel evenly around its center point. An unbalanced engine wheel can cause vibrations that can be felt throughout the vehicle.
- Dynamic balance: Dynamic balance ensures that the engine wheel does not wobble when rotating at high speeds. This is achieved by balancing the wheel both statically and by compensating for any imbalances that occur due to the wheel's rotation. An unbalanced engine wheel can cause vibrations that can damage the engine and other components.
Balancing engine wheels is a crucial part of engine maintenance and repair. By ensuring that the engine wheels are properly balanced, mechanics can help to extend the life of the engine and improve its overall performance.
Frequently Asked Questions (FAQs) About Engine Wheels
This section addresses common questions and misconceptions about engine wheels, providing informative answers to enhance understanding.
Question 1: What is the primary function of an engine wheel?An engine wheel, also known as a flywheel, plays a crucial role in converting reciprocating motion into rotational motion within an engine. It stores kinetic energy during the power stroke and releases it during the exhaust and intake strokes, ensuring continuous rotation of the crankshaft and smooth engine operation.
Question 2: What materials are commonly used for engine wheels, and why?Engine wheels are typically made of cast iron or forged steel due to their inherent properties. These materials offer durability, strength, wear resistance, and heat resistance, enabling them to withstand the demanding conditions and forces encountered within an engine.
Question 3: How does the size of an engine wheel impact its performance?The size of an engine wheel is directly related to the size and power of the engine it is designed for. Larger and more powerful engines require larger engine wheels to handle the increased forces and store more kinetic energy, ensuring smooth and efficient operation.
Question 4: Why is it important to balance engine wheels?Balancing engine wheels is crucial for minimizing vibrations and ensuring efficient operation. An unbalanced engine wheel can cause excessive vibrations, leading to premature wear and tear of engine components and reduced overall performance.
Question 5: What are the consequences of using an unbalanced engine wheel?An unbalanced engine wheel can lead to a range of negative consequences, including increased vibrations, reduced engine performance, premature wear of components, and potential damage to the engine and other parts of the vehicle.
Question 6: How often should engine wheels be inspected and balanced?Regular inspection and balancing of engine wheels are essential for maintaining optimal engine performance and longevity. The frequency of inspection and balancing may vary depending on factors such as the type of engine, operating conditions, and manufacturer recommendations.
These FAQs provide a concise overview of key aspects related to engine wheels. Understanding these concepts contributes to a better comprehension of engine operation and maintenance practices.
Transitioning to the next article section...
Tips Regarding Engine Wheels
To ensure optimal performance and longevity of engine wheels, consider the following tips:
Tip 1: Regular Inspection and Balancing
Regularly inspect and balance engine wheels to identify and correct any imbalances. This helps minimize vibrations, reduce wear and tear, and improve overall engine operation.
Tip 2: Proper Material Selection
Choose engine wheels made from durable materials such as cast iron or forged steel. These materials can withstand the high stresses and temperatures encountered in engine operation.
Tip 3: Appropriate Size
Select an engine wheel size that is appropriate for the engine's power and application. A properly sized wheel ensures efficient energy storage and release, contributing to smooth engine operation.
Tip 4: Professional Installation
Entrust the installation of engine wheels to qualified professionals. Correct installation techniques are crucial for proper wheel alignment and balance.
Tip 5: Preventative Maintenance
Implement a preventative maintenance plan that includes regular checks for loose bolts, cracks, or damage on the engine wheel. Prompt attention to any issues can prevent costly repairs or replacements.
Tip 6: Avoid Excessive Loads
Operate the engine within its specified load limits to prevent excessive strain on the engine wheel. Overloading can lead to premature wear and potential damage.
Tip 7: Monitor Temperature
Monitor engine temperature closely, as excessive heat can weaken the engine wheel and compromise its performance. Address any overheating issues promptly.
Tip 8: Consider Upgrading
In high-performance applications or for engines with modified power outputs, consider upgrading to a lightweight flywheel. This can improve engine response and reduce rotational inertia.
By following these tips, you can enhance the performance, reliability, and lifespan of engine wheels, contributing to overall engine efficiency and longevity.
Transitioning to the article's conclusion...
Conclusion
In summary, the engine wheel, also known as a flywheel, plays a pivotal role in the smooth and efficient operation of an engine. Its primary function is to convert reciprocating motion into rotational motion, ensuring continuous crankshaft rotation and overcoming the uneven torque produced by the piston.
The material, shape, location, function, size, and balance of the engine wheel are all crucial factors that contribute to its overall effectiveness. Proper material selection, appropriate sizing, and precise balancing are essential for minimizing vibrations, reducing wear and tear, and ensuring optimal performance.
Understanding the importance of engine wheels and implementing proper maintenance practices, such as regular inspection, balancing, and preventative measures, are key to extending their lifespan and maximizing engine efficiency. Whether in the context of standard engines or high-performance applications, engine wheels remain a fundamental component that contributes to the overall reliability and longevity of engines.
Article Recommendations
- Unveiling The Delightful World Of Livewithkellyandmarkcom Recipes
- Comprehensive Guide To Stonehouse Management Unlocking Best Practices
- The Future Of Conflict Resolution Exploring Mediacioacuten Virtual
Also Read


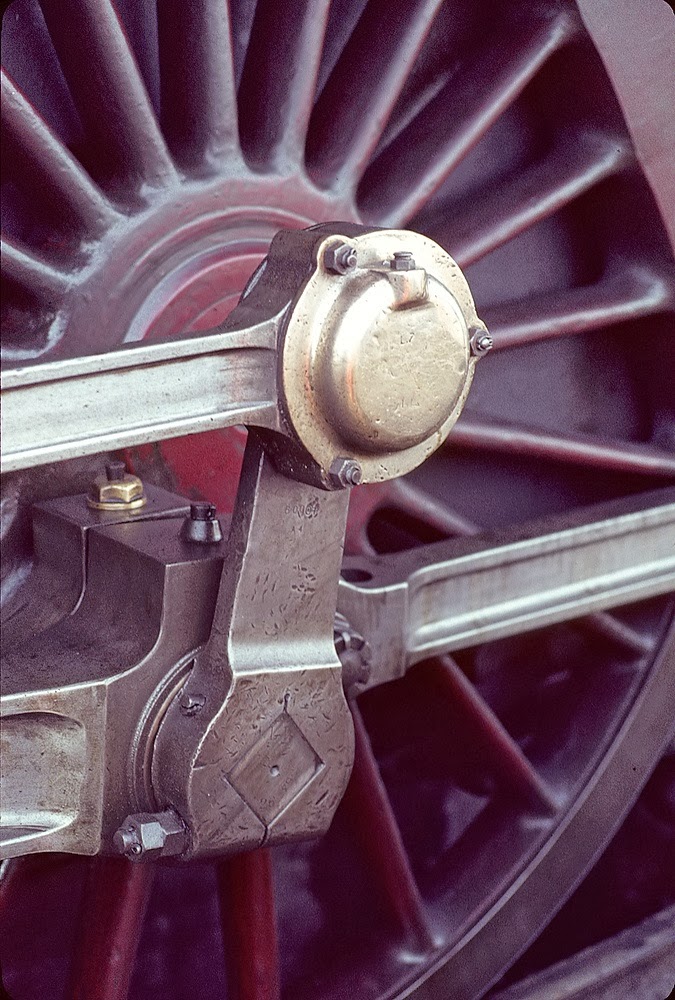